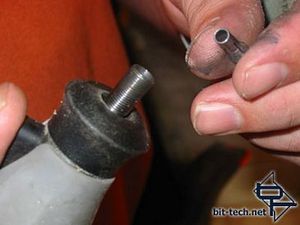
To finish up this I\'m going to switch over to the flex-shaft accessory to show how it works. It is the perfect time to do us this too because the handle on the flexshaft is thin and easy to hold close to what you are working on. That way the disk is perpindicular to the material. You can easily do this with the dremel itself but the bulkiness of the body sometimes makes you cut at an angle. First, we remove the cutting bit. Then, we remove the chuck and the retaining piece inside.
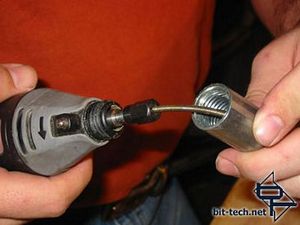
Then remove the accessory collar.. and replace the bit chuck with one that comes with the flexshaft.
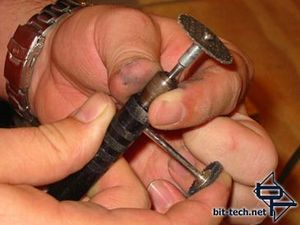
Then the flexshaft base screws onto the dremel accessories collar threads and the bit retaining piece and chuck is then moved to the end of the flexshaft. (I use a spare bit to hold the spindle still, it has a little hole you have to put something in to act as a stop any other dremel bit fits in there)
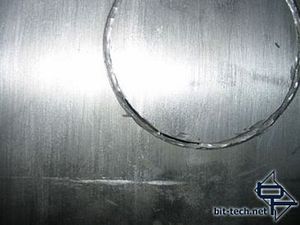
Now we have this smaller handle to deal with. One note of caution. I found that, mentally, when I have the dremel in my hand I am aware that it is a power tool and I am careful of the teeth at the end. However, when I am using the flexshaft, it feels like any normal tool and you tend to forget what is spinning at the end and there really isn\'t much from preventing your hand from slipping right down there so be careful. Another thing is that the speed controls for the tool isn\'t right there at your fingertips anymore. To get the flexshaft to work right, you need a decent amount of tension in the line running to the dremel so I hang mine up on my work area so to turn the tool off, I have to reach up, justkeep a mind of where it is in case you have to quickly turn it off. And onto lap #3, we are starting to see the other side of the tunnel, the disk is penetrating to the other side of the panel. A closer look in the lower pic.
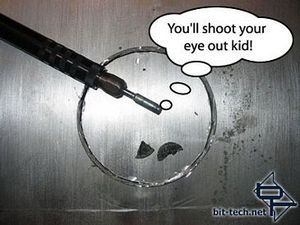
Here we go, reason #42 to wear your eye protection. While were on the subject, note the fine aluminum powder. It gets on everything including the lining of your lungs if you\'re not wearing a mask. This particular situation sucks because I really like having the cutting wheel at this size (remember, I was still on my first one) because it is perfect for getting in those tight places. When I am done with a job like this, I will replace the wheel with a new one when starting a new project and pull it out the used/smaller one for the more precise jobs.
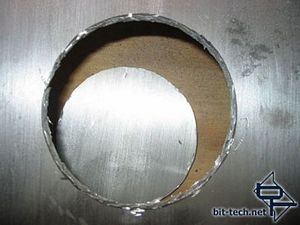
But alas, we had to put a new wheel on and finish the job. We\'re through the hole now with some pretty ugly looking edges. I\'m not about to just reach in there with my delicate hands and grab the disk. We need to clean this puppy up.
Want to comment? Please log in.